Guilda Masterbatch Flowboard Magazine
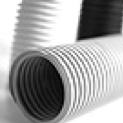
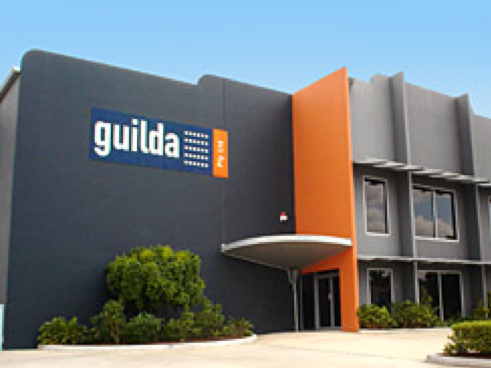
Injection molding machines have many components and are available in different configurations, including a horizontal configuration and a vertical configuration. However, regardless of their design, all injection molding machines utilize a power source, injection unit, mold assembly, and clamping unit to perform the four stages of the process cycle. Injection unit The injection unit is responsible for both heating and injecting the material into the mold. The first part of this unit is the hopper, a large container into which the raw plastic is poured.
Magazine Newsletter. NPE2018 New Technology Focus: Compounding. This device mates to an extruder; a small amount of the melt flow is diverted, measured and returned to the extruder to facilitate on-line analysis and adjustment of shear and elongational viscosities. An Australian colour masterbatch company, Guilda Pty Ltd, commissioned a long term UV weatherometer testing program to be undertaken on four of the most popular tank colours in Australasia. Guilda supply colour masterbatches to Australasian and Asian compounders.
The hopper has an open bottom, which allows the material to feed into the barrel. The barrel contains the mechanism for heating and injecting the material into the mold. This mechanism is usually a ram injector or a reciprocating screw.
A ram injector forces the material forward through a heated section with a ram or plunger that is usually hydraulically powered. Today, the more common technique is the use of a reciprocating screw. A reciprocating screw moves the material forward by both rotating and sliding axially, being powered by either a hydraulic or electric motor. The material enters the grooves of the screw from the hopper and is advanced towards the mold as the screw rotates. While it is advanced, the material is melted by pressure, friction, and additional heaters that surround the reciprocating screw. The molten plastic is then injected very quickly into the mold through the nozzle at the end of the barrel by the buildup of pressure and the forward action of the screw.
This increasing pressure allows the material to be packed and forcibly held in the mold. Once the material has solidified inside the mold, the screw can retract and fill with more material for the next shot.
Injection molding machine – Injection unit Clamping unit Prior to the injection of the molten plastic into the mold, the two halves of the mold must first be securely closed by the clamping unit. When the mold is attached to the injection molding machine, each half is fixed to a large plate, called a platen. The front half of the mold, called the mold cavity, is mounted to a stationary platen and aligns with the nozzle of the injection unit. The rear half of the mold, called the mold core, is mounted to a movable platen, which slides along the tie bars. The hydraulically powered clamping motor actuates clamping bars that push the moveable platen towards the stationary platen and exert sufficient force to keep the mold securely closed while the material is injected and subsequently cools. After the required cooling time, the mold is then opened by the clamping motor.
An ejection system, which is attached to the rear half of the mold, is actuated by the ejector bar and pushes the solidified part out of the open cavity. Injection molding machine – Clamping unit Machine specifications Injection molding machines are typically characterized by the tonnage of the clamp force they provide. The required clamp force is determined by the projected area of the parts in the mold and the pressure with which the material is injected. Therefore, a larger part will require a larger clamping force. Also, certain materials that require high injection pressures may require higher tonnage machines. The size of the part must also comply with other machine specifications, such as shot capacity, clamp stroke, minimum mold thickness, and platen size.
Injection molded parts can vary greatly in size and therefore require these measures to cover a very large range. As a result, injection molding machines are designed to each accommodate a small range of this larger spectrum of values. Sample specifications are shown below for three different models (Babyplast, Powerline, and Maxima) of injection molding machine that are manufactured by Cincinnati Milacron. The injection molding process uses molds, typically made of steel or aluminum, as the custom tooling. The mold has many components, but can be split into two halves.
Each half is attached inside the injection molding machine and the rear half is allowed to slide so that the mold can be opened and closed along the mold’s parting line. The two main components of the mold are the mold core and the mold cavity. When the mold is closed, the space between the mold core and the mold cavity forms the part cavity, that will be filled with molten plastic to create the desired part. Multiple-cavity molds are sometimes used, in which the two mold halves form several identical part cavities. Mold overview Mold base The mold core and mold cavity are each mounted to the mold base, which is then fixed to the platens inside the injection molding machine. The front half of the mold base includes a support plate, to which the mold cavity is attached, the sprue bushing, into which the material will flow from the nozzle, and a locating ring, in order to align the mold base with the nozzle.
The rear half of the mold base includes the ejection system, to which the mold core is attached, and a support plate. When the clamping unit separates the mold halves, the ejector bar actuates the ejection system.
The ejector bar pushes the ejector plate forward inside the ejector box, which in turn pushes the ejector pins into the molded part. The ejector pins push the solidified part out of the open mold cavity. Mold base Mold channels In order for the molten plastic to flow into the mold cavities, several channels are integrated into the mold design. First, the molten plastic enters the mold through the sprue.
Additional channels, called runners, carry the molten plastic from the sprue to all of the cavities that must be filled. At the end of each runner, the molten plastic enters the cavity through a gate which directs the flow. The molten plastic that solidifies inside these runners is attached to the part and must be separated after the part has been ejected from the mold. However, sometimes hot runner systems are used which independently heat the channels, allowing the contained material to be melted and detached from the part. Another type of channel that is built into the mold is cooling channels. These channels allow water to flow through the mold walls, adjacent to the cavity, and cool the molten plastic. Mold channels Mold design In addition to runners and gates, there are many other design issues that must be considered in the design of the molds.

Firstly, the mold must allow the molten plastic to flow easily into all of the cavities. Equally important is the removal of the solidified part from the mold, so a draft angle must be applied to the mold walls. The design of the mold must also accommodate any complex features on the part, such as undercuts or threads, which will require additional mold pieces. Most of these devices slide into the part cavity through the side of the mold, and are therefore known as slides, or side-actions. The most common type of side-action is a side-core which enables an external undercut to be molded. Other devices enter through the end of the mold along the parting direction, such as internal core lifters, which can form an internal undercut.
Guilda Masterbatch Flowboard Magazines
To mold threads into the part, an unscrewing device is needed, which can rotate out of the mold after the threads have been formed. Mold – Closed.
Comments are closed.